Titanium metal powder – the possible revolution in titanium manufacturing
What is titanium metal powder? You know about titanium in its metal form, about titanium in titanium dioxide, but probably you want to know about this newer titanium powder thing. As a product, it looks like a common metal powder, with the color ranging form grey to black. It has an apparent density of 1.4 g/cm3 and mostly keeps every property of the base metal.
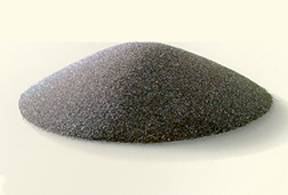
One of the most common titanium properties is its unmatched corrosion resistance. This is caused by the passive oxide layer that is formed automatically when pure titanium reacts with oxygen from atmosphere. This reaction is caused by titanium’s great affinity with oxygen which also leads to titanium being more readily found in nature as titanium dioxide, and not in its pure metal form.
Usually, one’s greatest strength is also its greatest weakness. This is also the case for titanium metal. The affinity for oxygen makes for some really cool properties, such as this corrosion resistance we talked about. But this also means that titanium is harder to process in pure metal form. More than 95% of the titanium metal mined today is in form of titanium dioxide – rutile or ilmenite, which must be reduced to metal form.
The most used commercial process for titanium reduction is the Kroll process is, among other things, say environmentally challenging, first and foremost, energy intensive, thus expensive. Titanium metal powder may be the answer for finally finding a way to produce pure titanium cheaper, allowing for an extended use in other applications, which are not feasible today because of the production costs. Just imagine bridges made out entirely of titanium metal. Not only would they be strong, but because of titanium lower weight, it will also need less structural support. Not to mention that the maintenance costs would be severely reduced, as titanium does not rust. No more paint, no more expensive check-ups. An indestructible bridge that will probably remain in place forever.
The second most important reason for further exploring of titanium metal powder production processes is its possible application in future manufacturing technologies. This method, which vividly resembles some sci-fi industrial robots, is based on the concept of adding consecutives layers of metal onto a temporary matrix in order to reach the intended final product; as opposed to the traditional methods which are based of taking out layers from a standardized piece of metal – an ingot or a slab, in order to obtain the desired form.
The advantages are obvious. Laser sintering produces no scrap. It requires no tooling or retooling. It allows for a far greater liberty of design than traditional methods. The efficiency of the process is close to 100%, assuming there are no errors. It is also a net-shape process meaning that the initial production of the item is very close to the final (net) shape, reducing the need for surface finishing. Reducing traditional finishing such as machining or grinding eliminates more than two-thirds of the production costs in some industries.
This method only works with metal powders, thus making the research and development of new production technologies for titanium metal powder a necessity.
The patented FFC Cambridge process may be the answer to this question. The FFC process was developed by Prof. Derek Fray, Dr. Tom W. Farthing and Dr George Zheng Chen at the University of Cambridge and works by placing a metal oxide in a molten salt bath heated to between 800°C and 1000°C, passing a current between it and a counter electrode. At the interface between the current collector, the salt and the metal oxide, the oxide ions leave the metal oxide and are carried across the salt to the anode, where they evolve as a gas. This leaves the pure metal behind.
The benefits of the FFC process over older pyrometallurgical technology, such as Kroll, are clear. Because it is a great deal simpler and requires a lower energy input, there are obvious reductions in energy consumed, carbon footprint and cost. An integrated 5,000 tone per year titanium production plant using the Kroll process will require a capital expenditure of £400m or more, while a plant based on the FFC process will cost in the region of £50 million.
For me it is clear than it is only a question of time until laser sintering and titanium metal powder becomes the standard in industrial manufacturing. In the mean time, titanium powder can make some really beautiful fireworks.
Return from Titanium metal powder to Titanium Industries
Return to Titanium Exposed Home Page